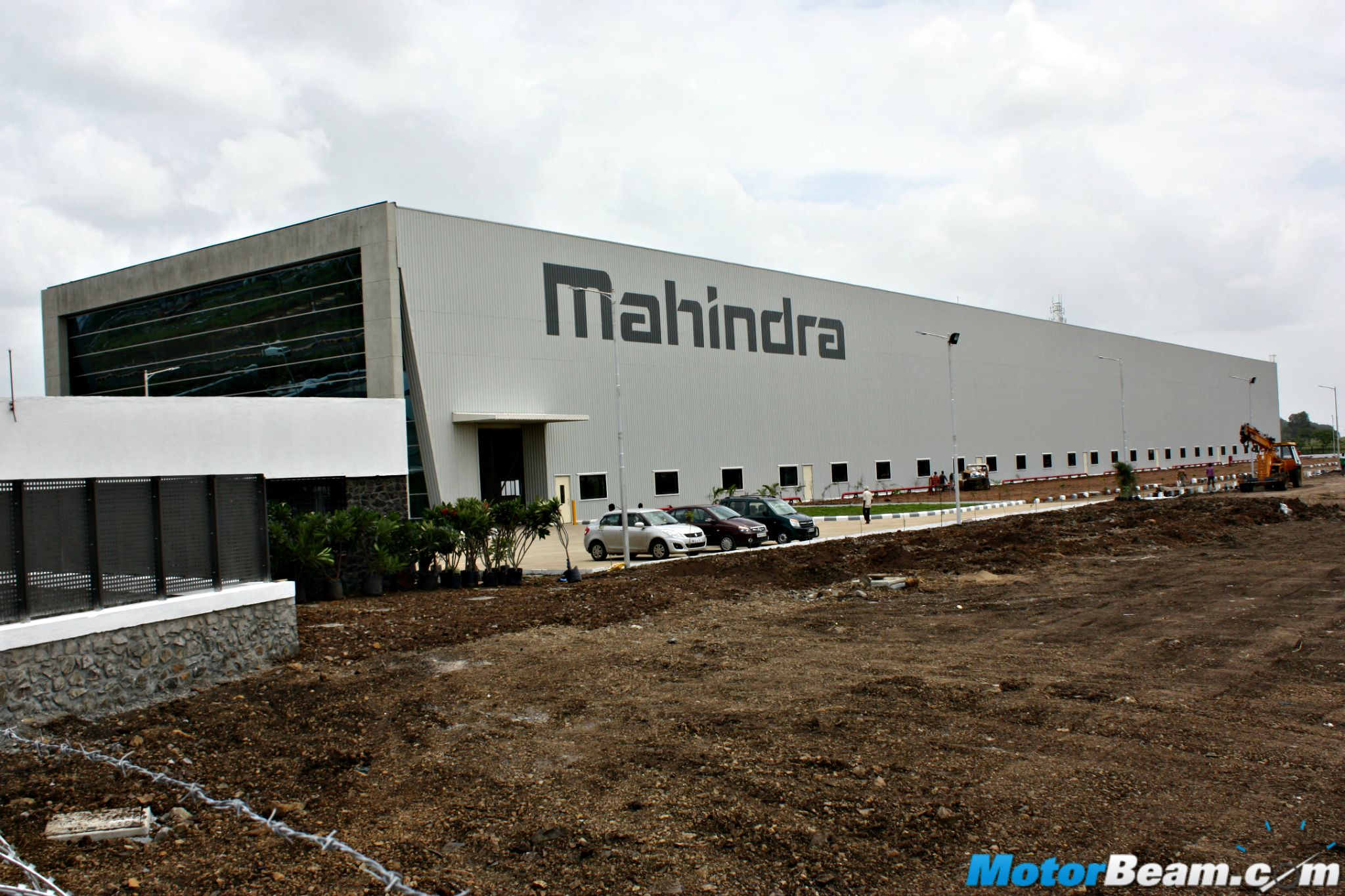
Mahindra’s new state-of-the-art fully automated facility optimises productivity with minimal effort
While Mahindra & Mahindra has made a name for itself in the automotive industry, few know that the company originally started out as an importer of steel in 1945 before assembling Jeeps post independence. Expanding horizons, Mahindra’s Intertrade division set up India’s first independent steel service centre in the organized sector in 1993 and gradually opened several more globally. With the growing demand in the auto sector, the Intertrade division recently opened its third Auto Steel plant in Pune sourcing raw material from domestic and overseas. Before the official announcement of the plant’s inauguration, Mahindra invited us to have a look at its newly constructed facility in Chakan near Pune and gave a glimpse of the state-of-the-art process for creating automotive body profiles on the blanking lines. What we essentially saw here was the very first step towards manufacturing the all-new TUV300.
The new plant is a JV between Mahindra, Mitsui & China Steel
The new Auto Steel plant is a joint venture between Mahindra Intertrade that holds 51% stake along with China Steel Global Trading Corporation, Taiwan and Mitsui & Co. (Asia Pacific), Singapore, both of which hold 24.5% stake respectively. Spread over 10 acres, the new facility currently uses just 7000 sq. metres and is set up with an investment of Rs. 110 crores. Future ready, the plant witnesses a highly automated process which Mahindra chooses to call ‘Human Machine Interface’ that minimizes the need for human involvement during the blanking process. It is one of the country’s most advanced plants in its sector and is capable of providing the highest tensile strength of steel measured at 980 mpa, ready for any kinds of demand from the clientele.
The plant can provide the highest tensile strength steel measuring 980 mpa
The all automated process makes for a peaceful environment
We entered the factory on a cloudy Monday morning and it was rather delightful to see the freshly painted structure soaking of novelty. After a quick presentation about the Intertrade division’s history and the plant’s origin in the conference room, we were taken to the actual plant just a door away. While our most plant visits include witnessing an extremely busy factory floor, this easily is one of the most silent factories that we have ever been to. Mahindra’s steel production facility takes a more eased out approach as work gets done in a completely automated fashion, reducing the need for human involvement. The plant’s total employee strength stands at around 20-30 at present.
The blanking line has India’s largest bolster measuring 5-metres long & 6-metres wide
The new auto steel plant has been set up for manufacturing blanks, trapezoids and profiles. The relatively hollow facility has the Fagor Arrasate blanking line sourced from Spain installed right in the centre while tonnes of unprocessed steel and multiple dies are stored at the back, waiting to be processed. The blanking line is one of the most advanced and also India’s first servo line that allows better control and precision on the machining process. The Fagor blanking line is also accredited for having the biggest bolster in the country that measures 5-metres long and 6-metres wide.
Raw steel rolls ready to be processed on the Fagor blanking line
The automated line produces 1.20-metres per second & 110 tonnes per year
As part of the process, the machine presses the sheet steel blanks in order to make body panels for cars. In our presence, the blanking line produced the rear inner door profile for the Mahindra TUV300 in the current shift, which were then packed and shipped off to the automaker’s production facility around 15 kilometres away. In addition, the line is flexible enough to cut trapezoidal blanks with a maximum angle of 35-degrees and runs at 90 strokes per minute at full speed. The state-of-the-art blanking line moves at 1.2-metres per second and can produce up to 1,10,000 tonnes of pressed steel every year.
The steel roll gets washed in oil ridding all impurities before being pressed and cut
Furthermore, the folks at Mahindra also conveyed that the plant follows ‘Level 3’ safety standards, which is better than the European factory standards with most following Level 2 gradation. The facility has also optimised production at the plant with the blanking line accessible to parent company Fagor online, which can troubleshoot any problems without having to physically send a personnel. Given the plant has just commenced operations, the automaker is running the facility on a single shift, but could increase the same based on demand.
The blanking line remains locked out during the process to avoid all human involvement
Mahindra is in talks with GM, VW, Tata & Fiat to supply auto steel
Speaking of which, Mahindra is currently in talks with several auto manufacturers in the vicinity to which it could supply pressed steel. Given the blanking line is capable of meeting multiple requirements, the automaker can optimise production for different manufacturers to meet their specifications. In case of the TUV300, the steel is pressed measuring 0.7 mm of thickness, 914 mm width of coil blank and 1456 mm of length for each blank, which also meets the crash test safety standards as per the company. Given its strategic location, Mahindra has the logistic advantage over rivals in the steel business thereby reducing the turnaround time for most auto manufacturers. In the Chakan-Talegaon belt, the steel manufacturer is looking at a clientele inclusive of Fiat, General Motors, Volkswagen and Tata Motors, in addition to providing steel for Mahindra’s products, each of which are spread at a maximum difference of 60 kms from the auto steel facility.
The finished inner door line for TUV300 ready to be shipped to Mahindra’s car plant.
Easily one of our most peaceful plant visits, the day was signed off with a delicious lunch as we bid farewell to Mahindra’s technologically advanced side that manages to surpass most players in the business. The new plant will be playing a major role in the company’s future operations and will act as a supply base for the automaker’s future products that will be manufactured at the Chakan production facility. Coming to expansion plans, while the company definitely has the space to increase operations, it does depend on how the market conditions and clientele demand. At present, the automaker is prepared to meet a promising future.
Mahindra’s new plant will solve logistic issues for several automakers in the region