The state-of-the-art BMW facility in Chennai is capable of churning out 11,000 units every year, assembling 50 percent of local content on essential German offerings.
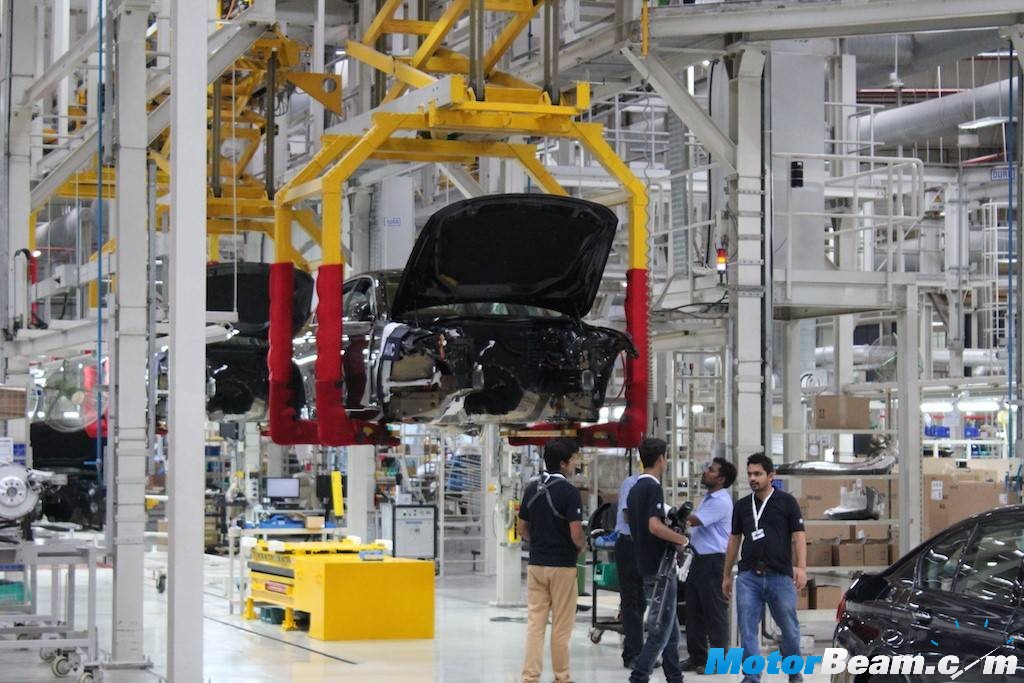
The 50% usage of local components at the facility showcases BMW India’s commitment
If you are even remotely interested in automobiles or any kind of mechanicals, a factory visit/plant tour can be an extremely interesting proposition wherein you are acquainted with the process of the vehicle manufacturing in front of your very own eyes. The feeling is no different than seeing a new life come to the world. Poetic if you look at it from an auto junkie’s perspective! So when we were asked to join BMW, one of the world’s driver focussed car makers for a visit at its state-of-the-art assembly plant in Chennai, it was certainly a thing to look forward to.
The BMW India facility started operations in 2007 and assembles 9 models via CKD route
We joined BMW for the celebrations of achieving 50 percent local content on its cars that coincides with the Prime Minister’s ‘Make In India’ initiative. With 50 percent localisation achieved, the Bavarian automaker made some special arrangements to commemorate the occasion with President Philippe von Sahr, the Chennai Plant Managing Director, Robert Frittrang and the cricket legend and BMW India’s brand ambassador Sachin Tendulkar gracing the event to create something special (more on that later). While Chennai’s mid-year heat had no plans of showing any respite that day, it surely didn’t dampen the excitement to check out where do those precise handlers with overwhelming amounts of power are actually made.
A bit of trivia on BMW’s Chennai facility, the German auto giant commenced operations at this plant on 29th March 2007 and has been assembling nine models from the company’s stable including the 1-Series, 3-Series, 3-Series Gran Tourismo (GT), 5-Series, the flagship 7-Series as well as the SUVs X1, X3 and X5. The ///M performance models and the i8 are brought in as Completely Built Units (CBU). The products are assembled on two lines at the plant as it ships out around 11,000 units a year.
The plant has 25 workstations for assembling & churns out around 11,000 units a year
The day kicked off with President Philippe von Sahr addressing the media that was followed by ace batsman Sachin Tendulkar stepping onto the factory floor to assemble a car. A first time at the plant for him as well, the cricketer disguised himself in the factory attire and teamed up with the officials to install locally sourced components on the 5-Series sedan (520d) that was being made on the assembly line. To that one customer who has unknowingly bought the 5-Series assembled by Sachin, you are one lucky bloke mate!
BMW India President Philippe von Sahr with Sachin Tendulkar at the factory floor
The BMW Chennai plant comprises of 25 workstations, each dealing with the different assembly of parts on the vehicle. The company sources the major components from Indian vendors which include –
* Engine and Transmission from Force Motors
* Axles from ZF Hero Chassis
* Door Panels and Wiring Harness from Draexlmaier India
* Exhaust Systems from Tenneco Automotive India
* Heating, Ventilating, Air-conditioning and Cooling Modules from Valeo India
* Mahle Behr and Seats from Lear India.
These components are then mounted on each of the vehicles through a mix of automated and manual assembly operations that work in tandem to get the job done every day. BMW officials at the plant said that the company continues to keep a certain section of the assembly process have the human touch that ensures its cars have a soul in addition to sheet metal. A car spends around 25-30 minutes on every workstation before moving to the final inspection process.
BMW has 6 major component suppliers that supply 50% of the local content on its vehicles
BMW imports the body on each of its vehicles in the country from its European facility and hence the paint section isn’t used for full-fledged paint jobs and is rather used for nips and tucks to the damaged parts. The paint section at the Chennai facility handles around 42 different colour shades and the officials also shared that only parts and panels with minuscule damage during transit are repainted before being installed on the car. Panels with extensive damage are completely replaced. The Indian plant follows the same colour code and paint quality as its European counterpart to maintain the same superlative levels of quality on its product range.
The Chennai facility’s paint shop is capable of handling 42 different colour options
The final inspection process comprises of checking the vehicle on several pointers before sending it for a road test. The process is divided into five sub-inspections with the first being static appearance where the car is checked for any physical or visual problems including paint job, scratches, part damages on the inside or outside. The following inspections are based on functionality that involves checking each and every component on the vehicle including the electricals, drivetrain, mechanical components among others.
The final inspection process is divided in 5 sub-sections covering every detail
Once the car has been assembled with all the preliminary checks made, parts installed and final inspection conducted, it is sent for a road test before being deemed fit as ‘Ready to be shipped’. In the road test, the vehicle is driven on the different sections of the track which include the Trapeze track, Sinus Wave track, 8 Loop, Warning Gauge and Cobble Stone tracks. The car is driven at an average speed of 20 km/hr and has the driver checking for any unnecessary noises or malfunctioning components which are then rectified immediately.
BMW conducts a stringent road test on every vehicle that is produced in the factory
Certainly a highly enriching experience, the BMW Chennai facility shows the company’s dedication towards creating cars that are not only luxurious and powerful but also have a soul in them. In business terms, the increased local content will help the company price its products more effectively against the competition while also improving the after sales and service with parts easily attainable on several major components. Certainly, it is as much a joy to watch a BMW come to life, as it is drive one.
BMW’s popular 3-Series is ready to be shipped to dealers after final tests
BMW Chennai Plant Tour Key Points –
1) BMW will soon assemble the 3.0-litre inline 6-cylinder diesel engine in India that powers a host of offerings in the company’s lineup.
2) The new X5M and X6M will be heading to Indian shores this year via the CBU route of course.
3) BMW will bring in the 1-Series facelift in the second half of this year that was unveiled ahead of the Geneva Motor Show.
4) The recently unveiled 3-Series facelift will also make it to India this year.