Established in 1976, Apollo Tyres has been one of the major players in the manufacture and sale of automotive tyres in India. With major acquisitions and setting up of manufacturing facilities, the company today is 16,000 employees strong across India, South Africa and Europe. There are four manufacturing facilities in India, one in Limda, Gujarat, which also happens to be the largest one, two in Kerala and the latest one near Chennai. The combined production capacity is 1400 tonnes a day. Apollo is also coming up with a green-field facility in Hungary which is slated to take the company to the next level. Currently, the company is Q1 supplier for Ford Motors and is also working on a collaboration model with Toyota for the upcoming second generation Innova.
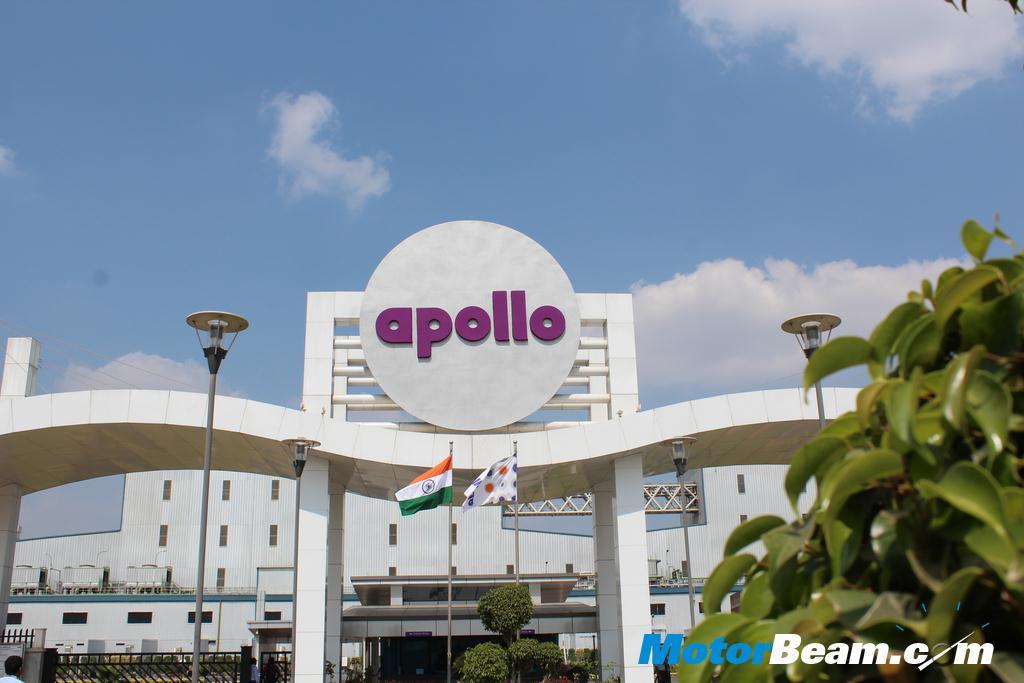
We had an opportunity to visit the Chennai facility recently and watching how a tyre was churned out of raw rubber was a treat to our eyes. The Chennai plant is Apollo’s largest green-field manufacturing facility that churns out all radial, passenger car (PCR) and truck bus tyres (TBR). 1600 employees strong, the facility is all set to increase truck bus radials production by 50 percent. The 3-layer structure for employees turned out to be a unique model being followed by a manufacturing plant. There was an aura of discipline everywhere as the company believes and follows a behavior based safety model. The plant is very well laid out which is evident from the fact that the PCR and the TBR units are on either side of the central spine which houses common units like coolers (both air and water type), offices etc. The company aims to be the Toyota of the tyre manufacturing industry which is indeed the right benchmark to target.
Our plant tour started with all of us getting into our safety shoes and jacket. We were first taken to the ‘Nerve Centre’. This houses the central management system which controls and manages the functioning of the entire plant. The layout, PCR and TBR SCADA system, UPS power monitoring system, IP network backbone, video surveillance system and the PIBS, Apollo’s SKU management system were housed in the Nerve Centre.
From there, we moved to the Process Control Laboratory where all the raw materials were tested for their physical and chemical properties. Watching the Mooney Viscometer, the various types of rubber (natural and synthetic) and various other equipment gave us a feeling of our own Chemistry labs in school. We got to touch and feel the Ribbed Smoke Sheet (RSS) used in making the tyres and the nylon and steel cords which are used as a reinforcement in the tyres.

With nostalgia sinking in after seeing all the chemicals, we moved to the DBP test room where we saw the fume head chamber. The mixing room gave us the complete insight into how the ‘Masters’ are made from raw rubber and converted to the ‘Final’. Huge sheets of masters lay all around us neatly folded and waiting in the queue for the next stage of processing. Most of the functions were automated. After going through the stock preparation area, we were finally taken to the passenger car manufacturing section. The complete process of extrusion was explained to us. Here, two or more sheets of masters are fed and single sheet of required thickness is obtained from the extruder.
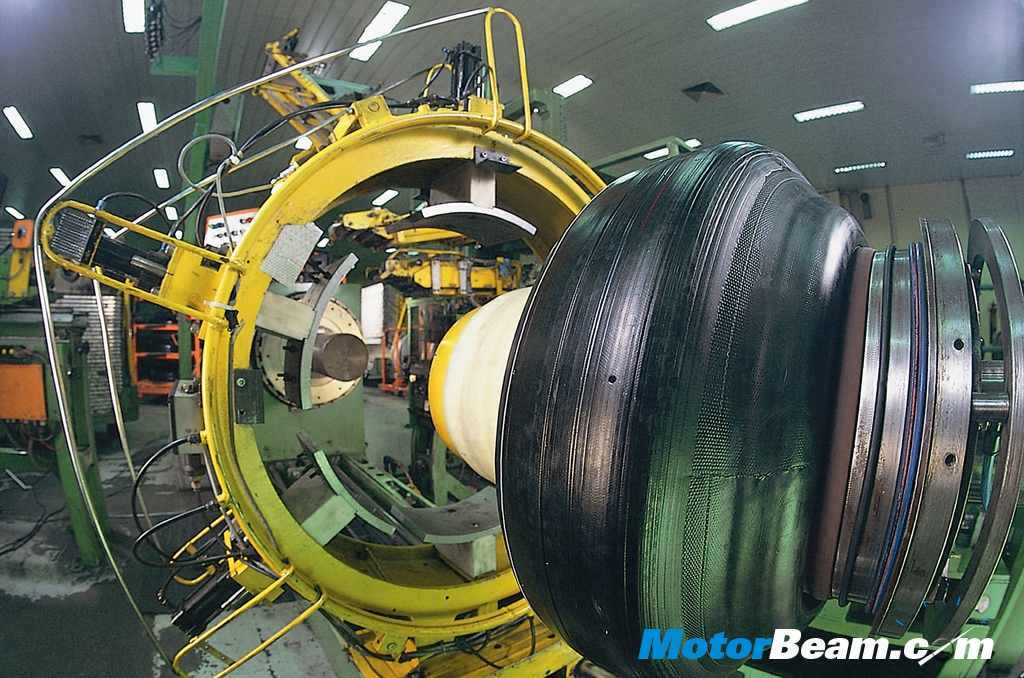
The most exciting part of this tour was the tyre building machine. A layer of inner liner would slide and sit on the roller and a layer of chafer would cover it along with the ply. The beads are set on either sides followed by turn-up and side wall attachment. After a final stitch, the carcass is ready. This carcass is fed into the shaping head where first belt, second belt, cap strips and treads are added and assembled and finally the green tyre emerges out as the output.
From here, we were taken to the unloading section, where these green tyres were fed into a steam based machine for curing. A rubber diaphragm maintains the shape of the tyre. The curing took different times for differently sized tyres. For instance, it took 7 minutes for a passenger car tyre while we were told that it takes close to 40 minutes in case of truck tyres. We were lucky enough to watch the final tyre emerge out of this machine which was indeed ‘smoking hot’, literally.
Though the Chennai plant is huge, we never felt exhausted even for a split second as every section of this plant was a new learning and essentially made us understand our vehicles and their tyres better. Adding to the excitement was the empathy shown by the Sun God which kept the temperature bearable during the visit.